Safety is Stuck – But It Doesn’t Have to Be
If you’ve been in construction for long enough, you’ve seen the big improvements in safety over the years. We've reduced minor injuries, tightened regulations, and implemented more controls than ever before. And yet, despite all the progress, serious incidents and fatalities haven’t gone away. In fact, in some cases, they’ve plateaued—or worse, stayed stubbornly high.
So, what’s going on?
The reality is, traditional safety methods (often called “Safety I”) have taken us as far as they can. They’re great at reducing frequent, low-consequence injuries, but they haven’t been as effective at preventing the big stuff—the major accidents that change lives forever.
This is where Safety Differently (also known as Safety II) comes in. This approach is heavily influenced by the work of thought leaders such as Sidney Dekker, Todd Conklin, and Erik Hollnagel, who have spent years studying the complexities of safety in high-risk industries. Rather than focusing solely on stopping things from going wrong, Safety Differently also emphasises learning from what goes right. And if that sounds a little different from how we’ve always done things, you’re absolutely right. But different doesn’t mean unproven. There’s a growing body of evidence showing that this approach works—and the best part is, you don’t have to throw out what already works to start benefiting from it.
What is Safety Differently?
At its core, Safety Differently challenges the idea that workers are the problem. Instead of assuming accidents happen because people aren’t following the rules, it asks, how do people succeed despite all the challenges they face every day?
Think about it:
- Your teams adapt constantly to changing site conditions, incomplete plans, and shifting deadlines.
- They solve problems in real-time, making decisions on the spot to get the job done while keeping things safe.
- And yet, our safety systems are mostly built on preventing failure, not understanding success.
By focusing only on what goes wrong, we miss a massive opportunity to learn from the times things go right. If we study how crews navigate risks successfully, we can build safer systems that support them—not just punish them when something goes wrong.
The Opportunity: Mini-Experiments, Big Impact
Now, let’s be real—nobody is suggesting we throw out hard hats and start taking unnecessary risks. Safety Differently isn’t about abandoning rules—it’s about making them smarter, more practical, and more adaptable to real-world conditions.
One of the most promising ways construction managers are testing this approach is through small, low-risk “mini-experiments”. These are practical, real-world trials where teams make small adjustments and see what impact they have on safety and productivity.
Here are a few examples of what that might look like:
- Learning from Work-As-Done: Instead of assuming the written procedure is always correct, shadow workers on site and see where reality differs. Then, adjust processes to support the way work actually gets done safely.
- Blameless Incident Reviews: When something goes wrong, instead of looking for a rule-breaker to blame, ask, what conditions made this failure possible? and how can we prevent it from happening again?
- Encouraging Near-Miss Reporting: Shift the mindset from “reporting gets people in trouble” to “reporting helps us all get better.” Many companies find that when they make this change, serious incidents drop because teams feel safe flagging risks before they turn into disasters.
- Simplifying Safety Paperwork: Some companies have experimented with reducing excessive safety documentation. Instead of thick binders of procedures, they create simple, clear guidance that crews actually use. The result? Higher compliance and fewer workarounds.
Each of these experiments is small enough to test without disrupting operations, but when you start stacking them together, you get a powerful shift in safety culture—one where people are engaged, thinking, and actively contributing to making the site safer.
The Challenges: Why Some Managers Hesitate
Now, let’s be honest—change is never easy. Some managers hear about Safety Differently and assume it means letting workers “do whatever they want.” That’s not the case.
Other common concerns include:
❌ “This sounds soft on safety.” Actually, it’s the opposite. Instead of chasing zero incidents (which can drive underreporting), Safety Differently focuses on eliminating serious accidents while improving real, day-to-day safety.
❌ “We already have a safety system in place.” That’s great—this approach doesn’t replace what you’re doing. It enhances it by adding practical ways to learn and adapt, making your system more effective.
❌ “How do we measure success?” Traditional safety metrics like injury rates don’t always show improvement right away, but leading companies are using new indicators—like increased near-miss reporting, better worker engagement, and fewer serious incidents—to track progress.
If you’re already running a safe site but want to take it to the next level, exploring Safety Differently through small, practical changes is a great place to start.
Let’s Work Together to Build Safer Construction Sites
At the end of the day, we all want the same thing: every worker going home safely at the end of the day. The question is, how do we get there?
As safety consultants, we work with construction professionals who see the potential of Safety Differently and are willing to try small, practical experiments to improve safety and performance. Our approach is grounded in the research and insights of leaders like Dekker, Conklin, and Hollnagel, applying their hard work in a way that makes sense for your business.
If that sounds like you, let’s talk. We’re looking to collaborate with companies that want to learn, experiment, and improve safety together.
Are you ready to take the next step? Let’s connect and start making safety work better for the real world.
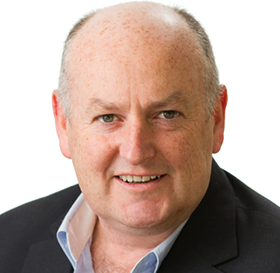