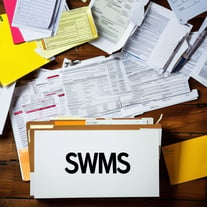
Transform your safety documentation from a tangled, convoluted mess into streamlined, efficient tools that not only enhance compliance but also significantly improve safety outcomes. By refining and organising your safety documents, you can create a clear and concise system that empowers your team to access vital information quickly and accurately. This transformation not only reduces the burden of excessive paperwork but also fosters a more proactive and engaged safety culture within your organisation. Through this meticulous approach, you ensure that every piece of documentation serves its purpose effectively, leading to a safer, more productive work environment where compliance is seamlessly integrated with everyday operations.
The Hidden Cost of Safety Clutter
Safety clutter refers to the unnecessary complexity and sheer volume of safety documentation that can bog down processes, inhibit clear communication, and ultimately diminish the effectiveness of safety measures intended to protect workers and enhance operational efficiency. When safety documents are overloaded with excessive information, it can lead to an environment where confusion reigns, productivity decreases, and a false sense of security takes hold. Critical information, which is vital for maintaining safety standards, often gets buried under layers of redundant or irrelevant details, making it difficult for employees to access what they truly need.
Moreover, the burden of excessive documentation can result in disengagement among workers and supervisors alike. When these individuals feel overwhelmed by the sheer volume of paperwork, they may become frustrated, leading to a situation where critical safety steps are inadvertently overlooked or bypassed. This hidden cost of safety clutter manifests in several detrimental ways: lower compliance with safety protocols, a decline in worker morale, and ultimately, a compromise of overall safety. It is essential to recognise and address these issues to foster a work environment where safety documentation supports, rather than hinders, the goal of maintaining a safe and productive workplace. By doing so, organisations can transform their safety culture into one that is proactive, engaged, and aligned with best practices.
Practical Steps to Simplify Your SWMS
Simplifying your Safe Work Method Statements (SWMS) begins with a thorough examination aimed at eliminating redundancy. This involves a meticulous review of your existing documents to identify and excise repetitive or superfluous information that may cloud the clarity of the procedures. The goal is to distill these documents down to their essentials, focusing on clarity by employing straightforward, concise language that is easy for all employees to comprehend, regardless of their role or expertise. This process of simplification not only enhances understanding but also ensures that critical safety instructions are easily accessible to everyone involved.
Once the redundancy is removed, the next vital step is to prioritise high-risk activities and controls within your SWMS. By directing your attention and resources towards areas that pose the greatest safety risks, you ensure that your SWMS remains not only focused but also highly effective. This targeted approach means that the most critical safety measures are communicated clearly and effectively, reducing the likelihood of oversight or error. To further enhance comprehension and retention of these procedures, consider incorporating visual aids such as flowcharts or diagrams. These tools can transform complex instructions into easily digestible visual formats, making it simpler for employees to grasp and follow safety protocols. By combining these strategies, you create a streamlined, impactful SWMS that supports a safer, more productive work environment.
Remember: Only hazards and risks that are directly related to High Risk Construction Work (HRCW) activities need be included in a SWMS. Non-HRCW hazards and risks may also be included if it is helpful to do so, however, this should not occur to such an extent that the intended focus on HRCW is lost.
At the end of the day, in addition to providing and maintaining a working environment that is safe and free of risks to health, so far as is reasonably practicable, you must also provide information, instruction and training. This information, instruction and training should be suitable and effective.
Identifying and Eliminating Common Safety Document Clutter
Common safety document clutter encompasses a range of issues that can hinder the effectiveness of safety management. These include overly detailed procedures that complicate rather than clarify, duplicated information scattered across multiple documents, and irrelevant or outdated content that no longer aligns with current practices or regulations. Such clutter can obscure critical information, making it challenging for employees to find the necessary guidance quickly and efficiently. To address this, a comprehensive review of your safety documents is essential. This involves systematically examining each document to identify and eliminate sections that add little value or could be merged with others to enhance clarity and usability.
For instance, when you find that multiple documents address similar safety procedures, it presents an opportunity to streamline by consolidating them into a single, comprehensive guide. This not only reduces redundancy but also simplifies access to vital information, ensuring that employees have a clear, singular reference point. Furthermore, it is crucial to establish a routine for regularly updating your documents. This practice ensures that your safety documentation remains relevant, reflecting the latest industry standards, technological advancements, and regulatory requirements. By doing so, you maintain a dynamic and responsive safety management system that supports both compliance and operational excellence.
Balancing Compliance with Effective Safety Management
Maintaining compliance while ensuring effective safety management requires a balanced and strategic approach that aligns with both regulatory demands and the dynamic needs of your workforce. To achieve this, it is essential to employ a variety of tools and techniques designed to enhance efficiency and clarity within your safety processes. Utilising safety checklists provides a structured method for ensuring all necessary protocols are followed consistently, while digital solutions offer a modern means to streamline documentation. These platforms not only simplify the process of updating and accessing crucial safety information but also facilitate real-time communication and data sharing across teams, ensuring that everyone is on the same page and can respond swiftly to any changes or updates.
Further, cultivating a flexible mindset is paramount. This involves embracing adaptability and being open to making adjustments based on valuable feedback from workers and real-world observations. By listening to those on the front lines and incorporating their insights, you ensure that your safety measures reflect the true nature of on-the-ground operations. This alignment of 'work as imagined' with 'work as done' helps bridge potential gaps between planned procedures and actual practices, ensuring that safety protocols are not only theoretically sound but also practically viable and effective in the field. Such an approach not only enhances compliance but also fosters a culture of continuous improvement and engagement, empowering your team to take ownership of their safety and that of their colleagues.
The Benefits of a Streamlined SWMS
A decluttered Safe Work Method Statement (SWMS) offers a multitude of significant benefits that extend beyond mere compliance. One of the primary advantages is the notable improvement in worker engagement. When safety documents are presented in a clear, concise manner, it becomes far easier for employees to comprehend and adhere to the outlined procedures. This clarity naturally translates into better compliance with safety protocols, as workers find it simpler to understand what is expected of them. Consequently, this leads to enhanced safety outcomes, as the likelihood of errors or omissions is significantly reduced.
Ideally, a streamlined SWMS serves as a catalyst for improved communication and collaboration within the workplace. By removing unnecessary complexity and focusing on essential information, these documents foster an environment where workers feel more empowered and confident in their roles. Such empowerment encourages a sense of ownership over their safety and that of their colleagues, cultivating a robust safety culture that prioritises vigilance and responsibility.
In addition to these benefits, simplified safety documentation supports the development of a proactive, performance-driven safety environment. This approach not only makes it easier for organisations to implement safety measures effectively but also ensures that every individual, from frontline workers to management, is aligned in their commitment to maintaining a safe workplace. Ultimately, the result is a harmonious work environment where safety becomes an integral part of everyday operations, benefiting not just the employees but the organisation as a whole.
Here’s a SWMS Declutter Checklist designed for construction safety professionals to improve the clarity, usability, and effectiveness of Safe Work Method Statements (SWMS). This checklist integrates the recommendations provided, balancing decluttering efforts with maintaining compliance and practicality.
Checklist Item | Goal | Yes/No |
1. Consolidation of Repetitive Sections | Review the document for any repeated information (e.g., PPE requirements, manual handling) and consolidate these into one section where appropriate. | |
2. Use of Tables for High-Risk Work (HRCW) | Ensure High-Risk Construction Work (HRCW) activities are clearly listed in a table format at the beginning, with associated risks and control measures. | |
3. Group Similar Hazards and Risks | Group related hazards and control measures (e.g., noise exposure, manual handling) into single sections to avoid redundancy. | |
4. Streamlined Control Measures | Focus on applying the hierarchy of controls, ensuring engineering and substitution controls are prioritized over administrative measures and PPE where feasible. Avoid repetitive mentions of PPE unless required for multiple tasks. | |
5. Assign Clear Responsibilities | Use a dedicated matrix to assign responsibility for implementing control measures, rather than embedding responsibility within each task section. | |
6. Emergency Procedures Specificity | Tailor emergency procedures to be site-specific but avoid listing them in multiple sections. Consider using flowcharts for clarity. | |
7. Minimize Overlap with Other Documents | Cross-check whether information already included in site safety plans, emergency procedures, or other documents is unnecessarily duplicated in the SWMS. | |
8. Simplify Language | Avoid excessive technical jargon. Use clear, simple, and concise language that can be easily understood by all workers, including those with limited safety training. | |
9. Eliminate Unnecessary Details | Review if every listed detail contributes directly to safety. Remove unnecessary background information or administrative details that do not add value to the task’s safety outcome. | |
10. Use Bullet Points and Lists | Replace large blocks of text with bullet points or numbered lists to increase readability, especially when listing steps or procedures. | |
11. Use Visual Aids | Where possible, replace text-heavy explanations with diagrams, flowcharts, or images to clarify complex tasks or processes. | |
12. Combine Consultation Records | Consolidate worker consultation records into one section rather than embedding them throughout the SWMS. Ensure consultation is documented but doesn’t overwhelm the document. | |
13. Highlight Critical Steps | Highlight or separate critical safety steps or controls (e.g., fall protection, crane operations) that require special attention. This helps workers focus on the most important actions. | |
14. Clear Triggers for SWMS Review | Specify concise and clear triggers for reviewing the SWMS (e.g., new risks, site conditions changes) in a single section instead of repeating the review requirement in multiple areas. | |
15. Use Digital Tools (Optional) | Where feasible, explore using digital tools for SWMS creation and updates to automatically reduce redundancy and ensure workers access the most current version of the SWMS. | |
16. Use a Summary Section | Provide a brief, high-level summary at the beginning of the SWMS outlining the scope, critical risks, and control measures. This allows workers to quickly grasp the key elements before diving into details. | |
17. Review for Unnecessary Compliance Burden | Ensure the SWMS is not overburdened with excessive "tick-box" requirements that don’t directly enhance safety. Focus on practical controls that will be followed in the field. | |
18. Ensure Alignment with Work-as-Done | Verify that the SWMS aligns with actual site conditions and work practices, addressing real risks and controls based on worker input. This helps prevent discrepancies between "work as imagined" and "work as done." | |
19. Verify Control Effectiveness | Include steps for verifying that the control measures remain effective throughout the task, ensuring the SWMS isn’t just a compliance document but a dynamic safety tool. | |
20. Regular Feedback and Revision Process | Implement a feedback loop for workers to comment on the SWMS clarity and practical use on-site, and adjust accordingly to maintain relevance. |
How to Use This Checklist:
- Before Writing: Use the checklist to plan the SWMS structure, ensuring that you are focused on practicality and ease of use.
- During Drafting: Check each section of your SWMS against this list to ensure it remains concise and clear.
- After Completion: Conduct a final review using the checklist to verify that the document is streamlined, easy to navigate, and compliant with regulatory requirements.
This decluttered approach to creating SWMS will help ensure the document is both regulatory compliant and practical, reducing unnecessary complexity while maintaining a focus on improving safety outcomes.
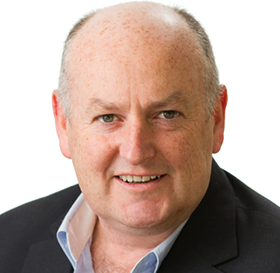