Conducting a gap analysis for ISO 45001 is an essential and profoundly insightful step in assessing the extent to which an organisation’s existing Occupational Health and Safety (OHS) management system meets the stringent requirements established by this international standard. This analysis not only provides a comprehensive overview of alignment but also serves as a diagnostic tool that highlights areas needing improvement. Common gaps identified during these thorough assessments often underscore significant deficiencies, particularly in critical areas such as documentation, leadership involvement, risk assessments, and the holistic integration of health and safety into everyday business operations. These gaps can inhibit an organisation's ability to fully leverage its health and safety initiatives, thereby impacting overall efficiency and employee wellbeing. In the following sections, I will provide a detailed examination of the most prevalent gaps, drawing from my experience in the field, insights from safety science literature, and established practices as outlined in resources like the OHS Body of Knowledge (BOK) and ISO 45001 guidelines. Through this exploration, organisations can gain a clearer understanding of the necessary steps to enhance their safety management systems, fostering an environment where safety is seamlessly woven into the fabric of their operational strategy.
1. Lack of Documentation and Record-Keeping
ISO 45001 places significant emphasis on maintaining comprehensive documented information for a variety of critical processes, including hazard identification, incident investigations, and ensuring legal compliance. This documentation serves as the backbone of a transparent and accountable Occupational Health and Safety management system. However, a prevalent gap that organisations face is the presence of missing or outdated documentation, which severely hampers their ability to demonstrate compliance with the stringent standards set by ISO 45001. Without accurate and up-to-date records, organisations struggle to provide evidence of their safety practices, which is essential for both internal reviews and external audits. Records of risk assessments, safety audits, and corrective actions are pivotal elements of this documentation. Yet, these records are frequently found to be incomplete or poorly maintained, leading to potential vulnerabilities in the safety system. Inadequate record keeping not only compromises the organisation's compliance status but also impedes the continuous improvement of safety practices, as it becomes challenging to track progress or learn from past incidents effectively. Therefore, maintaining meticulous and current documentation is not merely a procedural requirement but a fundamental aspect of fostering a culture of safety and accountability.
Recommendation:
Organisations should review their OHS documentation systems to ensure records are comprehensive, up-to-date, and easily accessible. This includes refining processes for keeping safety manuals, audit reports, risk registers, and incident investigation outcomes.
2. Inadequate Leadership Involvement
ISO 45001 mandates a robust and unwavering commitment from leadership towards health and safety management. This commitment goes beyond the mere approval of policies; it requires a proactive and hands on approach where leaders are deeply involved in setting strategic safety objectives, continuously reviewing performance metrics, and fostering an organisational culture that prioritises safety as a core value. Leadership must not only endorse safety initiatives but also champion them, demonstrating an active role in driving safety forward through visible participation and advocacy. Unfortunately, many organisations still fall short in this area, with senior management often demonstrating a disengaged attitude, perceiving safety obligations as just another compliance checkbox rather than integrating them as a pivotal component of the organisation's strategic framework. This limited engagement results in missed opportunities to harness the full potential of safety as a driver of business success and employee wellbeing, underscoring the need for a paradigm shift in how leadership views their role in health and safety management.
Recommendation:
Leadership should actively engage in the safety management system, including setting clear safety objectives, regularly reviewing OHS performance, and visibly supporting safety initiatives. Coaching leadership in understanding their role in promoting a positive safety culture is also key.
3. Ineffective Risk Assessments
Risk assessments serve as a critical pillar within the ISO 45001 framework, providing the essential groundwork upon which a robust Occupational Health and Safety (OHS) management system is built. Despite their importance, an alarming number of organisations either bypass this crucial step or execute it inadequately. This oversight can lead to significant vulnerabilities within the safety system. A frequent issue is the insufficient identification of potential hazards, which leaves organisations exposed to risks that could have been mitigated with a more thorough analysis. Additionally, there is often a lack of meaningful worker involvement in the risk assessment process. This exclusion not only diminishes the quality of the assessments but also overlooks the invaluable insights that employees, who are intimately familiar with the day-to-day operations, can provide. Compounding these challenges is the tendency to rely heavily on outdated risk matrices that no longer reflect the current operational environment or emerging threats. Furthermore, many organisations fail to regularly review and revise their risk assessments, an essential practice to ensure that they remain relevant in the face of evolving conditions, technological advancements, or new hazards that may arise. This negligence can lead to outdated safety protocols that fail to protect the workforce adequately, ultimately hindering the organisation's ability to foster a safe and supportive working environment.
Recommendation:
Risk assessments should be dynamic, involving all relevant stakeholders, and regularly updated. Incorporating worker insights, utilising advanced risk evaluation techniques, and ensuring proper risk control measures are in place are critical for compliance.
4. Insufficient Worker Participation
ISO 45001 places a significant emphasis on the critical role of worker consultation and active participation in the processes of safety management. This standard recognises that those who are directly involved in daily operations bring invaluable insights and practical knowledge of potential risks that may not be immediately apparent to those not on the ground. Despite this, a prevalent issue that organisations face is the absence of well defined and structured mechanisms to effectively incorporate employees into the decision making processes related to safety. This gap often results in workers feeling disengaged and undervalued, as their firsthand experiences and observations of on-the-ground risks are not fully utilised. Such underutilisation not only diminishes the quality of safety strategies but also overlooks opportunities to harness the collective expertise of the workforce, which is essential for anticipating and mitigating potential hazards. In essence, without structured avenues for worker participation, organisations miss out on a wealth of practical insights that could significantly enhance the effectiveness of their safety management systems.
Recommendation:
Establish structured ways for workers to contribute to safety decisions, such as safety committees, workshops, or learning teams. Utilising methods like humble inquiry to encourage open dialogue between safety professionals and workers can help bridge the gap between work as imagined and work as done.
5. Insufficient Incident Investigation and Learning Processes
Many organisations engage in incident investigations; however, these often take the form of fault finding missions rather than opportunities for learning and improvement. The primary focus tends to be on pinpointing individual mistakes or assigning blame, which can inadvertently create a culture of fear and defensiveness among employees. This approach overlooks the complex interplay of factors that contribute to incidents, such as systemic issues, environmental conditions, and process failures. As a result, the investigations fail to uncover the underlying root causes that are critical to preventing future occurrences. Consequently, similar incidents are likely to recur, as the organisation has not implemented effective measures to address the foundational issues. This cycle of blame not only stifles open communication and hinders the sharing of valuable insights but also misses the chance to transform these events into powerful learning experiences that could significantly enhance organisational safety and resilience.
Recommendation:
Adopt a more learning focused approach to incident investigations, ensuring that investigations explore systemic issues and encourage open participation without fear of punishment. Learning from incidents should inform safety strategies, including updates to risk assessments and control measures.
6. Ineffective Control Measures
Many organisations implement safety controls to mitigate risks and ensure a secure working environment. However, these measures are not always subjected to regular and rigorous testing or maintenance, which is essential for sustaining their effectiveness. As time progresses, various factors such as wear and tear, environmental changes, and evolving operational demands can cause these controls to deteriorate or become obsolete. This degradation can significantly elevate the level of risk, potentially compromising the safety of the entire workforce. The lack of a systematic approach to verify and validate these control measures represents a substantial gap in safety management. Without consistent evaluation and updates, organisations may find themselves relying on outdated or ineffective safety protocols that fail to protect employees adequately. Therefore, implementing a robust system for the continual assessment and enhancement of safety controls is crucial in maintaining a high standard of occupational health and safety, ensuring that the measures in place are both reliable and responsive to changing conditions.
Recommendation:
Regularly verify and validate the effectiveness of safety controls through routine testing, audits, and field inspections. Incorporating performance metrics that track the completion and effectiveness of control activities can help ensure ongoing compliance and risk mitigation.
7. Over-reliance on Safety Clutter
Safety clutter refers to the accumulation of unnecessary rules, procedures, or paperwork that do not meaningfully contribute to enhancing actual safety within an organisation. This clutter can become a significant barrier to effective safety management by introducing complexity and confusion into compliance processes. As a result, it can considerably reduce worker engagement, as employees may feel overwhelmed or demotivated by the sheer volume of redundant tasks that seem to have little practical relevance. Furthermore, safety clutter can dilute the focus on genuinely critical safety measures, diverting attention and resources away from initiatives that truly safeguard employees. Ultimately, this overabundance of irrelevant safety protocols can hinder the organisation's ability to foster a proactive and clear-headed approach to occupational health and safety, making it crucial to streamline processes and eliminate unnecessary elements that do not add value.
Recommendation:
Identify and eliminate safety clutter by critically evaluating each safety process's contribution to actual safety outcomes. This can be done by applying frameworks like the Three Cs: Contribution, Confidence, and Consensus.
Addressing these common gaps is critical to aligning with ISO 45001 and enhancing overall safety performance. Organisations need to build strong leadership involvement, foster a culture of continuous learning, and ensure robust worker participation. By focusing on dynamic risk assessments, control verification, and eliminating safety clutter, companies can move from mere compliance to creating a genuinely safe working environment.
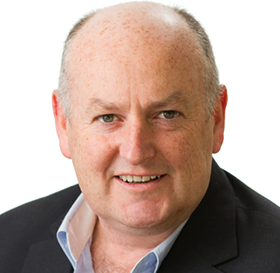