Why Manufacturing Safety Needs a Shift in Thinking
Manufacturing is one of the most high-risk industries (Safe Work Australia Manufacturing Safety Statistics), with workers exposed to hazards such as heavy machinery, hazardous chemicals, repetitive strain injuries, and high noise levels. While compliance with Work Health and Safety (WHS) regulations is essential, focusing solely on rules and enforcement is not enough.
To create a truly safe and productive workplace, managers must embrace a human-centric approach (Our approach Human-Centric Safety)—one that sees workers as part of the safety solution rather than the problem. By partnering with safety consultants who understand manufacturing’s unique challenges, managers can improve workplace safety, enhance operational efficiency, and build a resilient safety culture.
Why a Human-Centric Approach to Safety Matters in Manufacturing
Traditional safety programs focus on minimising human error through rules, procedures, and strict compliance. However, modern research in Human and Organisational Performance (HOP) and Resilience Engineering shows that workers are not the weakest link—they are the strongest defence against accidents.
Key Principles of Human-Centric Safety
Workers as Problem Solvers, Not Hazards
- Instead of punishing workers for non-compliance, organisations should listen to workers and identify why unsafe practices occur.
- Workers are often the first to notice safety risks—their insights should be valued.
Focus on Systems, Not Just Individuals
- Safety failures are rarely caused by a single worker mistake—they are usually systemic issues (e.g., unrealistic deadlines, poor communication, or inadequate equipment).
- Safety consultants assess organisational factors contributing to risks, not just individual behaviour.
Resilience Over Perfection
- It’s impossible to eliminate every risk in manufacturing. Instead, workplaces must be designed to adapt to change and recover quickly from incidents.
- Safety consultants help build flexible systems that support worker decision-making rather than relying solely on rigid procedures.
How Safety Consultants Support Manufacturing Managers
A safety consultant’s role is to help managers develop a practical, worker-focused safety strategy—one that improves compliance, enhances productivity, and protects workers.
1. Identifying High-Risk Activities in Manufacturing
Safety consultants conduct on-the-ground risk assessments (Comprehensive Manufacturing Safety Audits), helping managers understand real-world hazards, including:
- Heavy machinery operation (e.g., forklifts, CNC machines, conveyor belts).
- Hazardous chemical handling (e.g., exposure to solvents, adhesives, toxic fumes).
- Repetitive strain injuries (e.g., manual assembly lines, lifting tasks). WorkSafe Victoria's Guide to Hazardous Manual Tasks
- Lockout/Tagout (LOTO) failures (e.g., maintenance accidents from unexpected machine start-ups).
- High-noise environments (e.g., manufacturing plants with constant machinery operation).
Example: Instead of just enforcing PPE rules, a consultant may investigate why workers avoid using PPE—it could be uncomfortable, inaccessible, or impractical for specific tasks.
2. Strengthening Safety Culture & Worker Engagement
A strong safety culture starts with worker engagement, not just policies. Safety consultants help managers build trust by:
- Encouraging open safety discussions instead of relying on top-down enforcement.
- Using Learning Teams—where workers collaborate to identify hazards and propose solutions.
- Promoting a Just Culture, where reporting hazards and near-misses is encouraged (How Learning Teams Improve Workplace Safety), not punished.
Example: Instead of blaming a worker for a forklift collision, a consultant would examine the system — was there proper training? Was the area too congested? Were deadlines pressuring workers to rush? How Psychological Safety Improves Workplace Performance
3. WHS Compliance Without Bureaucratic Overload
Navigating Australian manufacturing safety laws (Safe Work Australia, ISO 45001, WHS Act) can be overwhelming. Safety consultants:
- Simplify legal compliance, ensuring policies are practical and easy to follow.
- Develop tailored WHS management plans, so compliance is built into daily operations, not just a checklist.
- Ensure Safe Operating Procedures (SOPS) are realistic and align with actual workflows.
Example: Instead of a generic WHS manual, a consultant customises safety protocols for each manufacturing process, ensuring they align with how workers actually operate on-site.
4. Incident Investigation & Learning from Mistakes
Instead of treating accidents as individual failures, a human-centric approach uses incidents as learning opportunities.
Safety consultants conduct in-depth investigations to:
- Identify systemic causes of workplace incidents rather than blaming individuals. (Incident Investigation & Root Cause Analysis)
- Provide corrective actions that address root causes, ensuring similar incidents don’t happen again.
- Implement realistic safety solutions that workers actively support.
Example: After a machine entanglement incident, a consultant examines the broader issue
Was the worker properly trained? Were the machine guards functional? Was the work schedule leading to fatigue?Key Safety Solutions for Manufacturing Managers
Safety consultants offer industry-specific services that help manufacturers prevent risks and ensure compliance.
- Manufacturing Safety Audits – Identify gaps in safety procedures.
- WorkSafe Compliance Support – Ensure full alignment with Australian WHS regulations. Our WHS Compliance Support for Manufacturing
- Risk Identification & Control – Assess high-risk activities like machine safety, hazardous material handling, and ergonomic risks.
- Safety Training & Workforce Engagement – Conduct learning-based safety programs for workers and supervisors.
- Incident Investigation & Root Cause Analysis – Shift from blame to learning, preventing repeat incidents.
- Development of WHS Management Systems – Implement tailored safety solutions that align with manufacturing workflows.
The Business Case for Human-Centric Safety
Many managers worry that prioritising safety slows down production—but the opposite is true.
A strong safety culture improves both safety and efficiency.
Key Benefits for Managers
- Fewer Incidents = Higher Productivity – Workplace accidents cause disruptions, legal issues, and lost time. How Proactive Safety Saves Money & Increases Efficiency
- Engaged Workers = Greater Retention – Workers who feel safe and valued are more productive and loyal.
- Legal Compliance Without Stress – Avoid fines and shutdowns by proactively meeting WHS requirements.
- Better Reputation = More Clients – Businesses with strong safety records attract better contracts and talent. Our Success Stories in Manufacturing
Safety is a Competitive Advantage
For manufacturing managers, safety is not just about compliance—it is about creating a workplace where workers thrive.By shifting from a rules-based approach to a human-centric model, managers can:
- Reduce accidents
- Improve efficiency
- Strengthen worker morale
- Ensure long-term success
Take Action Today
Looking for expert safety consultants for your manufacturing facility?
Our specialists at Work Safety Hub help managers implement practical, worker-focused safety solutions that improve compliance and productivity.
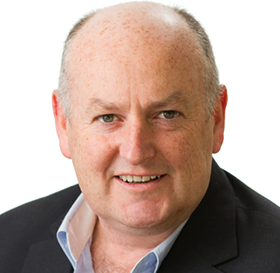